Maximizing Result and Reducing Downtime: The Essential Role of a Trusted Packaging Maker
A reliable product packaging equipment is not just a gear in the wheel yet a cornerstone that can considerably influence functional effectiveness, cost-effectiveness, and eventually, the bottom line of any organization. The dependence on a trustworthy product packaging device transcends mere capability; it is a keystone of making sure constant product top quality and conference consumer demands.
Importance of Reliable Product Packaging Makers
Reputable packaging equipments are the keystone of efficient production procedures, guaranteeing seamless operations and minimal disturbances in the packaging sector. These makers play an important role in keeping high levels of productivity and top quality standards within product packaging facilities. By purchasing trustworthy packaging equipments, business can minimize costly downtime, boost output ability, and improve general effectiveness.
One secret value of reputable packaging makers is their ability to constantly meet production needs. These makers are made to run constantly with marginal errors, bring about a steady circulation of packaged items without unforeseen disturbances. This integrity is important for fulfilling and meeting limited target dates customer orders quickly.
In addition, reliable packaging machines add to set you back financial savings in the lengthy run. In essence, the value of trustworthy product packaging makers can not be overstated in a highly affordable sector where effectiveness and high quality are critical.
Influence On Functional Effectiveness
Enhancing functional performance via the use of trustworthy packaging machines is important for sustained performance and streamlined procedures in the product packaging market. Dependable product packaging equipments play a vital function in ensuring that assembly line run smoothly and without interruptions, ultimately influencing the general operational performance of a packaging center.
By lessening downtime due to failures or malfunctions, trustworthy packaging equipments assist in maximizing production schedules and meeting consumer demands properly. This, consequently, leads to raised output and greater levels of client satisfaction. In addition, dependable makers contribute to cost savings by minimizing the demand for regular fixings and maintenance, therefore boosting the overall earnings of the procedure.
Furthermore, trusted packaging makers make it possible for packaging business to keep regular quality requirements in their items. By ensuring exact and precise packaging procedures, these equipments aid in minimizing errors and waste, additional boosting functional performance. Overall, the effect of trustworthy product packaging machines on operational efficiency is substantial, making them a foundation for success in the packaging market.
Expense Cost Savings and ROI
Attaining significant price financial savings and a desirable return on financial investment (ROI) is a critical objective for packaging companies aiming to take full advantage of operational effectiveness. By investing in trustworthy product packaging makers, business can decrease general production costs through increased efficiency, lowered downtime, and reduced upkeep costs. packaging machine repair. The preliminary in advance investment in a top quality packaging equipment might appear significant, but the long-term price financial savings and enhanced ROI make it a financially audio choice
Trustworthy packaging machines add to set you back savings by minimizing product waste, enhancing production procedures, and improving product quality control. These variables directly impact the lower line by decreasing expenses related to rework, turned down products, and ineffective use resources. Furthermore, the enhanced functional effectiveness provided by trusted product packaging machines results in raised outcome degrees, satisfying customer demands a lot more properly and potentially expanding market reach.
Ultimately, the price savings and enhanced ROI arising from buying a reputable product packaging device not just warrant the initial funding expense however likewise position the business for long-term success in an open market landscape.

Protecting Against Production Downtime
Decreasing manufacturing downtime is a critical aspect of preserving operational effectiveness in product packaging centers. To stop manufacturing downtime, aggressive upkeep timetables need to be developed for product packaging equipments.
Implementing predictive upkeep strategies, such as resonance evaluation and thermography, can additionally assist in recognizing potential issues prior to they rise right into significant issues. Educating device operators on proper usage and upkeep treatments is critical in protecting against preventable downtime caused by human mistake.
In addition, having a backup plan in position for emergency scenarios, such as accessibility to backup makers or spare parts, can significantly lower the period of any kind of unexpected downtime. By focusing on precautionary upkeep procedures and preparedness approaches, product packaging facilities can operate efficiently and maximize their output efficiency.
Making Certain Constant Product Top Quality
To keep a competitive side out there, packaging centers need to prioritize rigorous top quality control procedures to ensure regular product top quality. Consistency in item high quality is critical for consumer fulfillment and brand track record. Achieving this uniformity requires a mix of elements, with the product packaging device playing a crucial function.
One key element of making certain constant item quality is the calibration and routine upkeep of the packaging equipment. Proper calibration makes sure that the machine operates within defined resistances, reducing variants in product packaging output. Routine upkeep helps stop unanticipated break downs that can bring about defects in the packaging procedure.
In addition, buying premium product packaging materials and monitoring their usage is necessary for maintaining consistent product high quality. packaging machine repair. Damaged materials can cause packaging problems or variances that influence the overall product presentation and stability
Carrying out durable top quality control procedures, such as real-time tracking you can try these out and examination systems, can additionally help identify and deal with any discrepancies in product high quality immediately. By focusing on these procedures, product packaging centers can maintain high criteria of item top quality, meet customer expectations, and strengthen their position in the market.
Conclusion
To conclude, dependable packaging machines play a critical function in making the most of output and minimizing downtime in manufacturing procedures. By making sure operational efficiency, cost financial savings, and stopping production downtime, these devices are important for maintaining consistent item high quality. Buying dependable product packaging makers not only improves total efficiency but additionally contributes to the long-term success and productivity of a production company.
Dependable product packaging makers are the cornerstone of reliable production procedures, making sure seamless procedures and minimal disturbances in the packaging sector. By investing in trusted product packaging machines, firms can decrease pricey downtime, increase result capacity, and boost overall effectiveness.
Moreover, trusted packaging makers enable product official website packaging firms find out here now to preserve regular quality criteria in their products. In general, the influence of dependable product packaging machines on operational performance is substantial, making them a foundation for success in the product packaging sector.
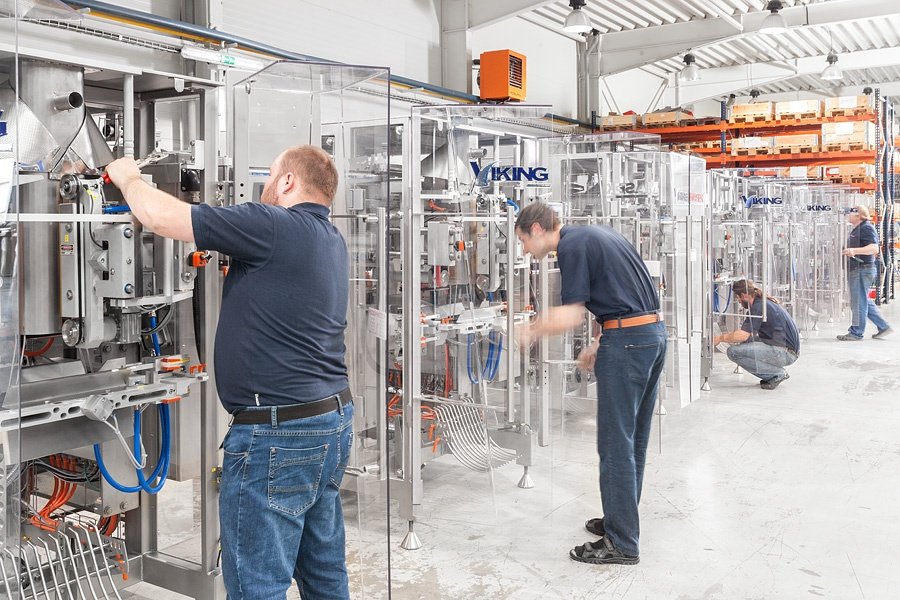